自动化的理论基础是控制论。控制论诞生时,控制论之父维纳思考了这样一个问题:机器和人(动物)到底有什么区别?维纳认为,机器一般只能按既定的步骤和逻辑运行,而人(动物)则能够通过信息感知到外部变化,并根据这些信息进行决策、采取行动。同样,自动化系统一般由传感器、控制器和控制对象构成,分别用于获得信息、决策和执行。因而,“感知、决策和执行的统一”可以看作是自动化的本质。
控制论的产生有个重要的技术背景,即弱电技术的产生和应用。强电一般是用来提供能量的,弱电则与信息技术有关。传感器测得的弱电信号用来表示信息,控制器用弱电进行计算和决策,同时,弱电又可以通过控制强电系统带动控制器的运行。这样,利用“电”这一技术手段,打通信息和物理世界,把信息世界的感知、决策和物理世界的执行统一起来,可以解决一般性的控制问题。
传感器获得的信号一般是模拟信号,即连续变化的信号。控制理论产生之初,控制器主要由电阻、电感、电容等电子元件搭建而成,可以直接处理模拟信号。与模拟量相对应的是数字量,一般是指用0、1二进制表示的数据,计算机存储和处理的数据、互联网传输的数据便属于此类。通过数模、模数转化,数字化信息和模拟信息可以相互转化。
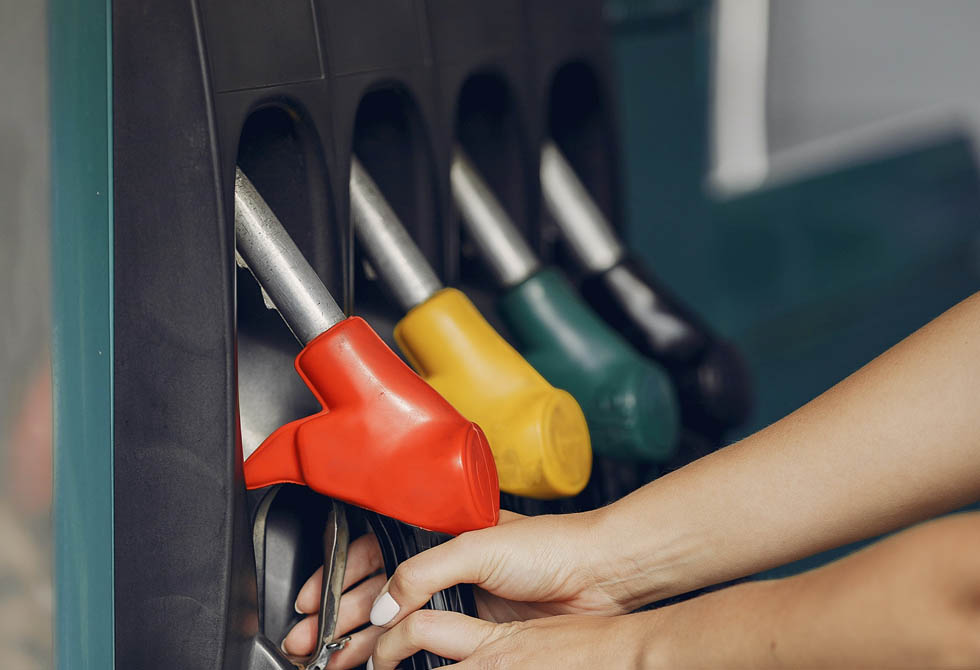
传统自动化技术取得了巨大的成功,但也有其局限性。比如,经典控制理论往往只是针对那些能用线性常微分方程组描述的物理对象,而许多物理系统不能用这类数学模型描述。另外一个局限是,自动控制往往只能针对结构和运行逻辑不发生变化的控制对象,如单台设备、阀门这样的小系统,这类其系统的结构和运行逻辑稳定是一种常态;而针对工厂这样的大系统,却难免出现某些设备故障、生产异常。对于上述问题,数字化方法具有巨大的威力。
数字化:
推进关键在于计算机和互联网的深入应用
推进数字化,其实就是要推进计算机和互联网的广泛、深入应用。
首先,数字化建模能力强大。利用计算机,人们有能力描述任何数学公式、物理对象以及生产和业务过程,工厂里的人、机、料等所有要素,都可以在数字化空间中加以描述。过去,受存储、处理能力的限制,这种能力无法充分释放。随着摩尔定律的延续,互联网、云计算、大数据等技术的产生,人们有能力在数字化的虚拟世界中完整描述制造企业的各种业务活动,并通过这个虚拟世界管理和控制物理世界。
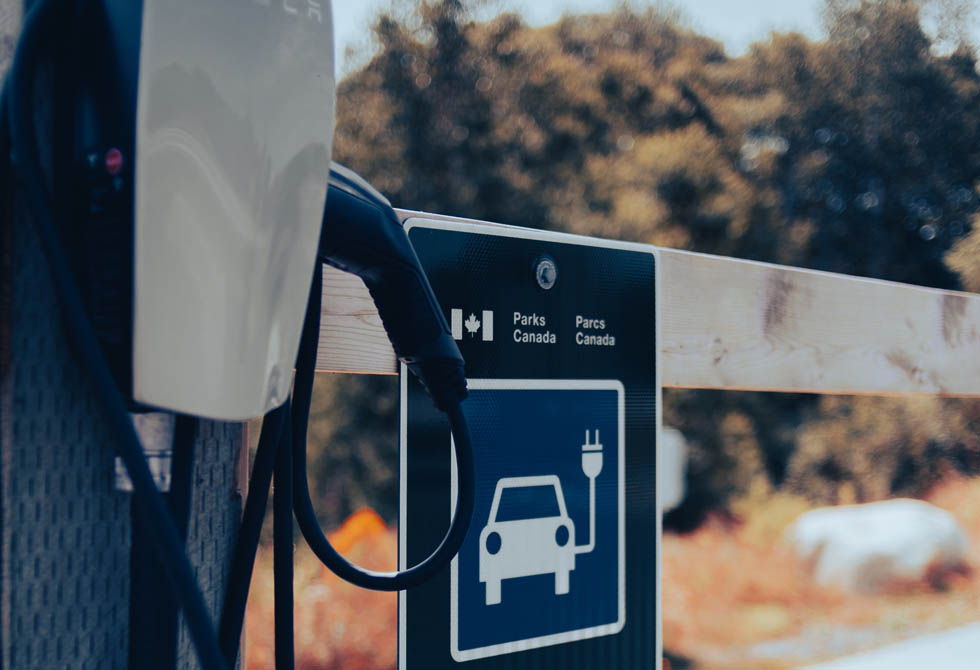
其次,计算机和网络系统可以帮助人类进行决策。无法实现自动控制时,一般需要人类专家(如调度人员、管理人员)进行处理。这时,这些系统能够帮助管理者获得信息、分析问题并传送指令,让人类能够更好地决策。从控制论的角度看,人类专家本质上是充当了一个“控制器”的角色。
制造企业的计算机系统往往是分级的。钢铁企业常见的做法是分成4级——L1~L4。其中,针对阀门、设备级系统进行控制的L1、L2系统一般被称为自动化系统;针对车间和工厂的L3、L4系统一般被称为“信息化系统”或者“管理计算机”。容易发现,层级低的系统往往反应速度快但管控范围小,层级高的系统反应速度慢但管控范围大。同时,低层级的计算机自动控制的比例高,高层级计算机自动控制的比例低。这种现象表明,对计算机系统来说,反应速度快、自动化程度高与管理范围大是矛盾的。
这种矛盾,对钢厂的管控是不利的。在钢厂里,能源、环保、质量、生产组织往往都会涉及多个部门和工序,属于大系统的问题。一个环节出现问题,往往需要大家协调解决。殷瑞钰院士经常说:“钢铁企业是典型的耗散系统。”如果问题处理得不及时,就可能导致能耗的增加、质量和生产效率的下降。然而,生产现场关键信息的出现是秒级、毫秒级的,而跨工序、跨部门的协调可能会耽误几个小时乃至几天。比如,连铸过程瞬间发生的问题,可能在几天后引发冷轧产品的质量缺陷。
在传统的计算机系统架构下,这类矛盾难以全面地解决,因为人类专家无法处理成千上万台设备和传感器发出的秒级、毫秒级的信息,而机器不擅长灵活处理跨工序、跨部门的大系统协同问题。这样的问题,需要在智能化时代,用数字化方法加以解决。
信息采编自网络,如有侵权,请于本站联系。